Materiales en aplicaciones de agua salada
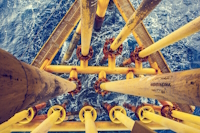
Figura 1: La corrosión es un problema inevitable en las aplicaciones de agua salada.
Varios materiales resistentes al agua salada son aptos para su uso en entornos marinos por sus propiedades únicas y su resistencia a la corrosión. Este artículo describe las características, ventajas e inconvenientes potenciales del acero inoxidable, el hierro fundido, el latón y el aluminio. Comprender estos factores es crucial para seleccionar el material ideal para una determinada aplicación en agua salada, ya sea en la costa, sobre el agua o sumergido bajo el agua.
Índice de contenidos
- Corrosión en ambientes salinos
- Metales en aplicaciones de agua salada
- PVC en aplicaciones de agua salada
- Cauchos en aplicaciones de agua salada
- Aplicaciones comunes de los materiales
- Preguntas frecuentes
Vea nuestra selección en línea de productos resistentes al agua salada.
Corrosión en ambientes salinos
La corrosión en un entorno marino es una preocupación importante debido a la naturaleza dura y altamente reactiva del agua salada. La corrosión en ambientes marinos se ve acelerada por la sal (cloruro sódico), que actúa como un excelente electrolito, facilitando el flujo de corriente eléctrica y acelerando los procesos de oxidación.
En entornos de agua salada pueden producirse varios tipos de corrosión.
- General: La corrosión general se produce cuando toda la superficie de un metal se corroe a un ritmo uniforme.
- Galvanic: La corrosión galvánica se produce cuando dos o más metales diferentes entran en contacto eléctrico en un entorno corrosivo. El metal más activo (anódico) se corroe a un ritmo acelerado, mientras que el metal más noble (catódico) queda protegido.
- Grieta: La corrosión en grietas es la corrosión localizada en lugares estancados, como los que se encuentran bajo juntas, arandelas, material aislante, cabezas de tornillos, depósitos superficiales y grietas en metales corroídos.
- Picaduras: La picadura es una forma de corrosión muy localizada que crea pequeños agujeros en el metal.
- Intergranular: La corrosión intergranular, un ataque selectivo en los límites de grano del metal, también puede producirse en determinadas condiciones, como cuando el metal se expone a condiciones corrosivas durante un periodo prolongado.
En cada caso, el proceso de corrosión puede provocar la pérdida de material, comprometiendo la resistencia y la integridad de las estructuras, equipos o recipientes, lo que puede dar lugar a fallos y accidentes. El coste económico de la corrosión es elevado y requiere importantes recursos para la sustitución y reparación del material corroído. Por lo tanto, comprender y mitigar la corrosión en entornos de agua salada es de vital importancia.
Aprenda cómo prevenir la corrosión en nuestro artículo sobre medidas anticorrosión para válvulas.
Metales en aplicaciones de agua salada
Esta sección trata de cuatro metales que suelen encontrarse en aplicaciones marinas. El siguiente cuadro ofrece una breve descripción y comparación entre los metales.
Tabla 1: Resumen/tabla comparativa de la idoneidad del acero inoxidable, la fundición, el latón y el aluminio en aplicaciones de agua salada
Tipo de metal | Coste relativo | Resistencia relativa al agua salada | Resistencia y durabilidad relativas | Ventaja principal | Principal desventaja |
Acero inoxidable | Alta | Alta | Alta | Gran resistencia a la corrosión y a las altas temperaturas | Costoso y no tan maleable como otros metales |
Hierro fundido | Medio | Bajo | Alta | Gran resistencia al calor y durabilidad | Susceptible a la oxidación |
Latón | Medio-Alto | Alta | Medio | Muy resistente a la corrosión, bueno para sistemas de agua caliente | No tan resistente como el acero, puede ser propenso a la desgalvanización |
Aluminio | Bajo | Medio | Bajo-Medio | Ligero, buena conductividad térmica y eléctrica | Menor resistencia, puede corroerse en ambientes muy alcalinos o ácidos |
Acero inoxidable
El acero inoxidable es un material muy adecuado para su uso en entornos de agua salada. Los factores del acero inoxidable que lo hacen fundamental en entornos marinos son:
- Resistencia a la corrosión: La principal característica del acero inoxidable es su notable resistencia a la corrosión, especialmente a la oxidación. Esto se debe principalmente a la presencia de al menos un 10,5% de cromo en su composición, que reacciona con el oxígeno para formar una fina capa invisible de óxido de cromo en la superficie del acero. Esta capa altamente adhesiva y no reactiva protege el acero de los elementos corrosivos, incluida el agua salada.
- Autocuración: Si se daña la capa de óxido de cromo, el cromo expuesto en el acero reaccionará con el oxígeno para restaurar la capa, proporcionando una propiedad de autocuración que no se observa en la mayoría de los demás metales.
- Durabilidad: El acero inoxidable es duradero, con gran resistencia a la tracción y robustez. Esto hace que sea capaz de soportar las duras condiciones de los entornos marinos, incluidos los impactos físicos que pueden producirse en estos entornos.
-
Variedad de grados: Los distintos grados de acero inoxidable marino están optimizados para diferentes entornos. Por ejemplo, el acero inoxidable 316, a menudo denominado acero inoxidable de calidad marina 316, tiene un elemento añadido, el molibdeno, que mejora su resistencia a los efectos corrosivos de la sal y otros productos químicos.
- Acero inoxidable de calidad marina 304 frente a 316: Aunque tanto el acero inoxidable 304 como el 316 se consideran aptos para aplicaciones de agua salada, los índices de corrosión del acero inoxidable 304 son mucho más elevados. Por lo tanto, el acero inoxidable 304 no es acero inoxidable para uso marino.
- Bajo mantenimiento: El acero inoxidable es fácil de limpiar y requiere un mantenimiento mínimo, lo que lo convierte en una opción rentable para su uso a largo plazo en entornos de agua salada.
Hierro fundido
El hierro fundido es un material importante para los productos utilizados en entornos de agua salada por las siguientes razones:
- Robustez y coste: El hierro fundido es robusto, pesado y duradero. Requiere un mantenimiento mínimo y su sustitución es rentable.
- Capa de óxido de hierro: Cuando el hierro fundido se expone al aire, forma de forma natural una fina y duradera capa de óxido de hierro en su superficie. Esta capa protectora protege el material subyacente de los efectos corrosivos del agua salada, ampliando su vida útil y manteniendo su integridad estructural.
El hierro fundido suele recomendarse para aplicaciones sobre el agua o cerca del agua. No se recomienda para aplicaciones subacuáticas porque es particularmente susceptible a la oxidación cuando está en contacto directo con agua salada durante periodos prolongados.
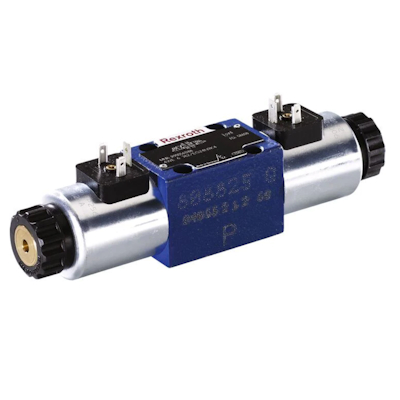
Figura 2: Una electroválvula hidráulica de hierro fundido
Latón
El latón es una aleación de cobre y zinc. Se utiliza en diversas aplicaciones, como accesorios marinos, sistemas de desalinización e intercambiadores de calor. El latón naval es una aleación de latón común utilizada en aplicaciones de agua salada. Se compone de un 59% de cobre, un 40% de zinc y un 1% de estaño, con trazas de plomo.
Dezincificación
El latón se empaña rápidamente cuando se expone al agua salada; sin embargo, puede mantener su integridad estructural. En algunas situaciones, sin embargo, el zinc puede eliminarse de la aleación, dejando sólo cobre, lo que reduce significativamente su integridad estructural.
Si aparecen manchas rojas, manchas minerales o una sustancia blanca en la superficie del latón, significa que ha comenzado la desgalvanización y que el componente de latón debe sustituirse lo antes posible. La desgalvanización se produce en ambientes contaminados y ácidos.
Si los componentes de latón pueden interactuar con un entorno que provoque la desgalvanización, existen varios métodos para ralentizar y mitigar el proceso. Un método habitual consiste en añadir arsénico a la aleación de latón naval cuando se fabrica el componente. Sin embargo, todo lo que se haga para proteger el latón contra la desgalvanización hace que el proceso sea más complejo y costoso. Por lo tanto, debe evitarse el latón si es probable que se produzca desgalvanización y se dispone de opciones de materiales más sencillos.
Aluminio
El aluminio se utiliza en entornos de agua salada por su ligereza y sus propiedades de alta resistencia. Además, el aluminio resiste bien la corrosión. Cuando se produce una pequeña corrosión, se forma de forma natural una fina capa de óxido de aluminio sobre la superficie corroída, lo que mitiga la corrosión posterior. Sin embargo, el agua y el aire salados pueden corroer más rápido de lo que puede desarrollarse la capa protectora en algunas condiciones. Esto puede producir picaduras en el aluminio.
La protección contra la corrosión del aluminio en agua salada es bastante sencilla. Tradicionalmente, basta con pintar la superficie del aluminio para protegerlo. Sin embargo, la pintura debe recibir un mantenimiento rápido siempre que se produzcan grietas u otros desperfectos. Sin embargo, más recientemente se ha desarrollado el recubrimiento en polvo. Esto crea una capa protectora dura sobre el aluminio, lo que reduce el mantenimiento con el paso del tiempo.
El aluminio no debe utilizarse directamente con metales más nobles como el cobre. Este contacto puede provocar fácilmente corrosión galvánica.
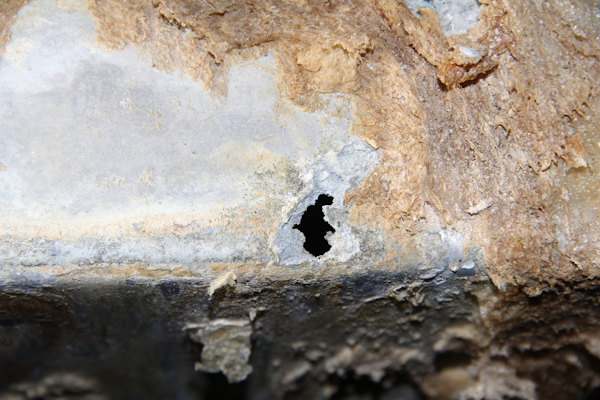
Figura 3: Corrosión en aluminio expuesto a agua salada estancada durante demasiado tiempo.
Aleaciones de aluminio para aplicaciones marinas
Las aleaciones de aluminio más utilizadas en aplicaciones de agua salada son las de aluminio-silicio, aluminio-magnesio y aluminio-magnesio-silicio.
- Al-Si: Las aleaciones de aluminio-silicio tienen una resistencia decente, lo que las hace adecuadas para su uso en bloques de motor. Añadiendo elementos como el cobre y el magnesio, estas aleaciones también pueden servir como relleno de soldadura. Se utilizan habitualmente para crear piezas de fundición a prueba de fugas y resistentes a la fatiga, así como piezas cruciales para usos marinos.
- Al-Mg: Las aleaciones de aluminio y magnesio no pueden tratarse térmicamente y son difíciles de moldear, pero resisten muy bien la oxidación, por lo que son ideales para piezas que entran a menudo en contacto con el agua de mar.
- Al-Mg-Si: La aleación de aluminio-magnesio-silicio es popular por sus cualidades estéticas y estructurales, y es ideal para los acabados. Se suele utilizar tanto en proyectos arquitectónicos de interior como de exterior. Estas aleaciones pueden tratarse térmicamente, tienen bastante resistencia, pueden moldearse con facilidad y resisten muy bien la corrosión.
PVC en aplicaciones de agua salada
El PVC y otros materiales plásticos han sido reconocidos desde hace tiempo como materiales adecuados para aplicaciones en agua salada debido a sus propiedades únicas que les permiten soportar el duro entorno del agua salada.
- Resistencia a la corrosión: El PVC es resistente a la corrosión del agua salada, lo que lo convierte en un material ideal para su manipulación en agua salada. A diferencia de las tuberías metálicas, que se erosionan con el tiempo debido a la exposición al agua salada, las de PVC mantienen su estructura y funcionalidad.
- No conductor: El PVC no conduce la electricidad. Se trata de una característica esencial en aplicaciones de agua salada, ya que el agua salada es un buen conductor de la electricidad. Así, el uso del PVC reduce el riesgo de accidentes eléctricos.
- Rentabilidad: Los componentes de PVC suelen ser más baratos que los metálicos. Además, al ser ligero, es más fácil y rentable de transportar e instalar. Por último, gracias a su resistencia a la corrosión, el PVC requiere menos mantenimiento, lo que reduce los costes a largo plazo.
El uso de PVC en aplicaciones de agua salada tiene sus desventajas:
- Sensibilidad a la luz solar: La exposición prolongada a la luz solar puede hacer que el PVC se vuelva quebradizo y se agriete con el tiempo.
- Baja resistencia química: El PVC tiene un rango relativamente estrecho de resistencia química. Por ejemplo, la exposición a disolventes orgánicos puede hacer que el PVC se reblandezca y pierda su forma.
- Temperatura y presión: El PVC suele tener valores nominales de temperatura y presión inferiores a los del metal. Puede soportar temperaturas de hasta 60 °C (140 °F) y presiones de hasta 13,8 bar (200 psi).
Cauchos en aplicaciones de agua salada
Los componentes del sistema que requieren un sellado (por ejemplo, las válvulas) necesitan que el material del sellado también sea adecuado para un entorno de agua salada. Los tres principales materiales utilizados son EPDM, caucho de neopreno y PTFE. Tenga en cuenta los siguientes factores a la hora de elegir:
- Coste: Si el presupuesto afecta significativamente a la selección del material, las juntas de caucho EPDM y neopreno suelen ser menos caras que las de PTFE.
- Resistencia al agua salada: Los tres materiales tienen una gran resistencia al agua salada. No hay diferencias significativas entre ellos.
- Resistencia al medio ambiente: El EPDM tiene mayor resistencia al ozono, a la intemperie y a la radiación UV que los otros dos materiales. Esto lo hace especialmente adecuado para aplicaciones exteriores en agua salada.
- Resistencia química: El PTFE tiene una mayor resistencia a los productos químicos que los otros dos materiales. Lea nuestra guía de resistencia química para obtener más información.
-
Rango de temperaturas: Los tres materiales, por término medio, tienen los siguientes rangos de temperatura:
- PTFE: -20 °C a 180 °C (-4 °F a 356 °F)
- EPDM: -50 °C a 120 °C (-60 °F a 250 °F)
- Neopreno: -40 °C a 120 °C (-40 °F a 250 °F)
-
Presión nominal: Los tres materiales tienen las siguientes presiones nominales:
- PTFE: 20 bar (290 psi)
- EPDM: 10 bar (145 psi)
- Neopreno: 15 bar (217 psi)
- Nota: Los rangos de temperatura y los valores nominales de presión están sujetos a cambios significativos en función de la estructura específica de la junta. Por lo tanto, utilice la información anterior como orientación general, pero consulte siempre con el fabricante del producto los valores específicos.
Aplicaciones de hidrocarburos
El EPDM y el neopreno son inadecuados para aplicaciones en las que intervienen aceites, gasolina y otros hidrocarburos. Sólo el PTFE es altamente resistente a estos medios.
Aplicaciones comunes de los materiales
Utilice los siguientes ejemplos de aplicaciones como guía para saber qué materiales elegir para los componentes del sistema, como válvulas y accesorios:
- Acero inoxidable: Las válvulas y accesorios de acero inoxidable pueden utilizarse en diversas aplicaciones de agua salada gracias a su resistencia a la corrosión. En la industria marítima, controlan el flujo de fluidos en barcos, submarinos y plataformas de perforación en alta mar. En las plantas desalinizadoras, gestionan el flujo de agua de mar y el agua dulce resultante.
- Hierro fundido: Las válvulas y accesorios de hierro fundido son menos resistentes a la corrosión que los de acero inoxidable. Se utilizan cuando se requiere resistencia y la exposición al agua salada no es constante. Pueden encontrarse en los sistemas de refrigeración por agua salada, en los sistemas de lastre de los buques y en determinados componentes de las plataformas marinas.
- De latón: Las válvulas y accesorios de latón son resistentes al agua salada y se utilizan en sistemas de fontanería marinos. Son habituales en los sistemas de refrigeración y calefacción de barcos, buques y plantas de tratamiento de agua salada.
- Aluminio: Las válvulas y accesorios de aluminio se utilizan a menudo en embarcaciones, especialmente cuando el peso es un problema. Pueden utilizarse en los sistemas hidráulicos de algunas embarcaciones ligeras o en acuarios de agua salada.
- PVC: Las válvulas y accesorios de PVC son muy resistentes al agua salada y se utilizan a menudo en aplicaciones marítimas en las que la resistencia a la corrosión es esencial, pero los componentes metálicos son innecesarios. Se utilizan mucho en sistemas de fontanería de agua de mar, plantas desalinizadoras e industrias de acuicultura para controlar el caudal de agua.
Preguntas frecuentes
¿Se oxida el acero inoxidable en agua salada?
El acero inoxidable es muy resistente a la corrosión del agua salada; sin embargo, acabará oxidándose y corroyéndose si se expone directamente al agua salada durante un periodo prolongado.
¿Es el latón resistente al agua salada?
El latón no es resistente al agua salada. Como mínimo, se empañará y, como máximo, sufrirá una desgalvanización que arruinará su integridad estructural. El latón naval es una opción más resistente.